Precautions for daily maintenance and inspection of screw air compressor
- Share
- publisher
- Michael Xu
- Issue Time
- Jan 9,2022
Summary
Precautions for daily maintenance and inspection of screw air compressor
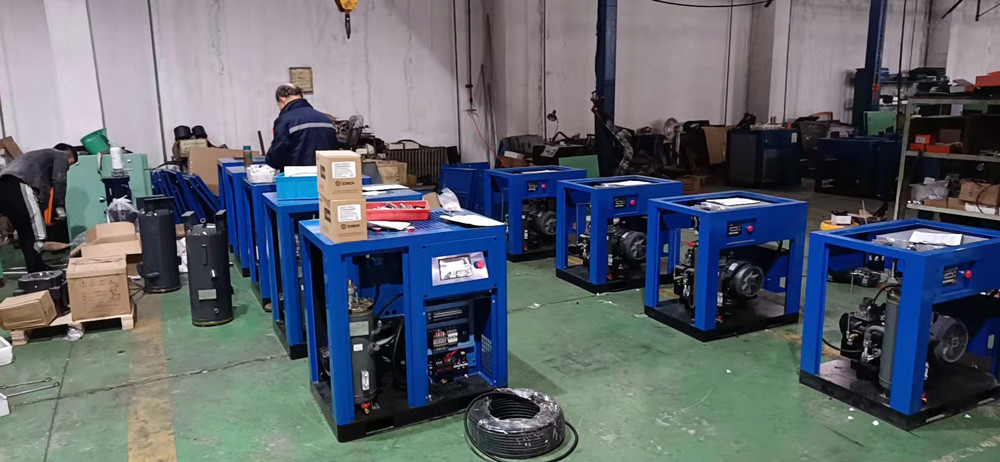
Precautions for daily maintenance and inspection of screw air compressor

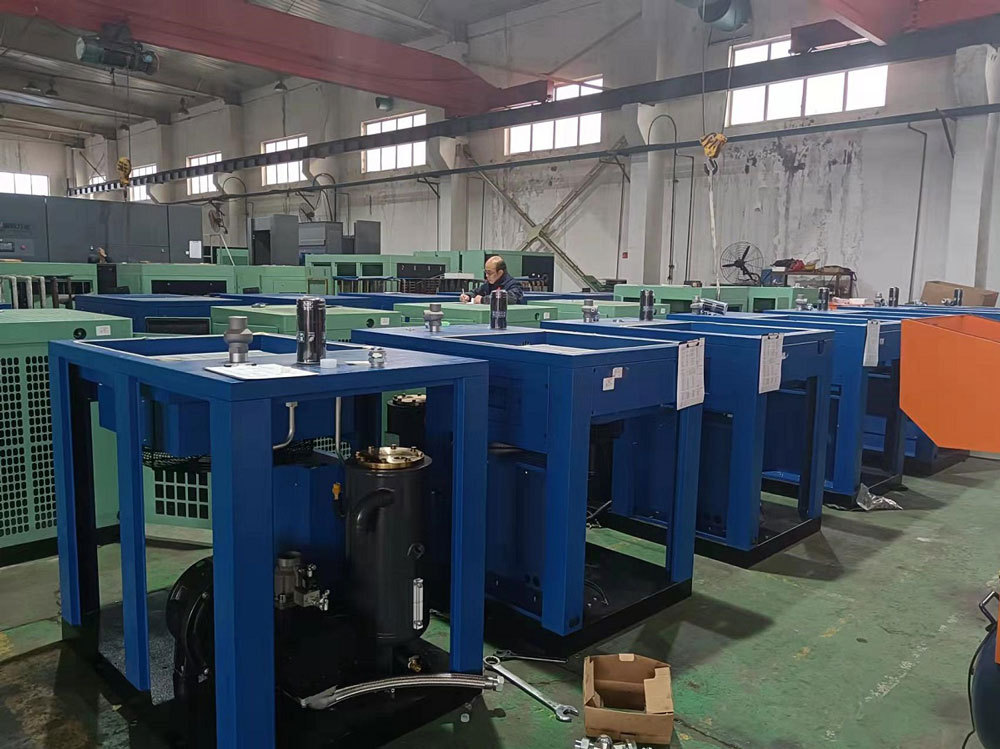
1. Specification and maintenance of lubricants
1. Lubricant
Lubricating oil has a decisive influence on the performance of oil-injected screw air compressors. If used improperly or incorrectly,
It will cause serious damage to the air compressor body. Please use the special oil specified and recommended by the manufacturer for the screw machine.
2. Factors affecting the oil change interval
1) Poor ventilation and high ambient temperature;
2) The relative humidity of the environment is high
3) The environment is dusty.
1. Oil change steps
1) Run the air compressor for a while to increase the oil temperature and reduce the viscosity of the oil, which is beneficial for discharge.
2) Press the stop button to stop.
3) When the oil and gas barrel has a pressure of 0.1Mpa, open the oil drain valve at the bottom of the oil and gas barrel. Due to the pressure,
The oil drain speed is very fast and it is easy to spray out, so it should be opened slowly to prevent the lubricant from splashing. After the lubricating oil has drained,
Close the drain valve. Note: All lubricating oil in the system must be drained, including pipelines, coolers, oil and gas
Barrels etc.
4) Open the oil filler plug and inject new oil.
4. Precautions for the use of lubricating oil
1) The scrapping and replacement of oil products depends on the old and new machine, the ambient temperature, humidity, dust and
Whether there is acid or alkaline gas in the air is related. Generally speaking, the new air compressor is replaced with new oil after 500 hours of use for the first time, the second time is 1000 hours, and the third time is the normal oil change every 2000 hours. The non-continuous operation of the air compressor should be changed in time.
2) Do not let the lubricating oil exceed the service life of the oil. The oil should be replaced on time, otherwise the quality of the oil
Decrease, poor lubricity, reduce the life of the head bearing. It is easy to cause high temperature shutdown phenomenon: at the same time because of oil
If the flash point drops, it is also easy to cause spontaneous combustion of the oil and cause the air compressor to burn down.
3) After the air compressor has been used for two years, it is best to use lubricating oil to do the oil "system cleaning" work.
The method is to replace the new lubricating oil, let the air compressor run for 68 hours, immediately change the lubricating oil again, and clean it thoroughly
There are various organic components remaining in the original system, so the replaced lubricating oil will have a longer service life
4) Lubricants of one grade should be added when refueling, and it is strictly forbidden to mix lubricating oils of different grades.
Second, the maintenance of the air filter
1) When prompted by the display or every 500 hours of operation, the air filter should be cleaned.
The compressed air blows away the dust from the inside to the outside.
2) The air filter element should be replaced every 2000 hours of operation.
3) Note: The cleaning or replacement cycle should be shortened when the environment is bad.
4) Note: When cleaning or replacing, strictly prevent foreign objects from falling into the intake valve to prevent the host from jamming.
Third, the replacement of the oil filter
1) The new machine should be replaced after 500 hours of operation for the first time
2) It should be replaced every 2000 hours after operation
3) It is better to change the oil filter when changing the oil
4) Note: The replacement cycle should be shortened when the environment is bad
5) Note: Replacement should be done after stopping the machine and releasing the pressure. When replacing, use a tool to unscrew the oil filter in a counterclockwise direction
core. The unscrewing process prevents lubricating oil from flowing to the base. When installing a new filter element, tighten it by hand. After the replacement,
It should be turned on and checked for leaks.
Fourth, the replacement of the oil fine separator
1) Under normal operation, the oil fine separator can work for about 200 hours, but the oil quality of the lubricating oil and the surrounding environment
The degree of pollution has a great influence on its life span. If the environmental pollution is very serious, consider installing a front air filter
Device
Generally speaking, whether the oil fine separator is damaged can be judged by the following methods:
a. The oil content in the air pipe increases.
b The pressure difference before and after the oil fine separator exceeds 012Mpa.
c Whether the current increases.
2) Safety precautions: The replacement should be carried out after stopping the machine and confirming that the system has no pressure.
2) The replacement method of the external oil fine separator is the same as the replacement method of the oil filter.
3) How to replace the built-in oil fine separator:
a Disassemble the piping of the upper cover of the oil and gas drum (including the piping between the outlet of the minimum pressure valve and the aftercooler);
b Remove the fastening screws of the upper cover of the oil and gas barrel.
c Remove the upper cover of the oil and gas barrel.
d Take out the fine oil separator and replace it with a new one.
e Install the oil and gas barrels in the reverse order of disassembly.
1) Note: There is an asbestos gasket on the top and bottom of the oil separator flange, and there are staples on the gasket.
The metal is a conductive sheet to prevent the generation of static electricity in the oil separator. The staples must be stapled as they are when replacing
2) Note: When installing, make sure that the distance from the oil return pipe deep into the oil and gas cylinder to the bottom of the oil fine separator is within 2-
3mm
3) Note: During the process of replacing the oil fine separator, it is necessary to prevent unclean items from falling into the oil and gas barrels
4) After the replacement is completed, the machine should be turned on to check for oil leakage
5. Maintenance period and content
Note: When it is a frequency conversion screw machine, it is best to choose D type circuit breaker.
Regarding the selection of transformers:
1. Normal star-delta start, the transformer capacity is more than 3 times.
2. When using soft start, the transformer capacity is 2.5 times or more.
3. When using a frequency converter, the capacity of the transformer is more than 1.5 times.
4. When using direct start, the transformer capacity is more than 5 times the rated power of the motor.