A Comprehensive Guide to Choosing the Right Fixed-Speed Rotary Screw Air Compressor
- Share
- publisher
- Leo Wang
- Issue Time
- Dec 19,2023
Summary
Selecting the perfect fixed-speed rotary screw air compressor involves a careful consideration of various factors. Let's embark on a detailed journey to ensure you make an informed decision tailored to your specific needs.

A Comprehensive Guide to Choosing the Right Fixed-Speed Rotary Screw Air Compressor
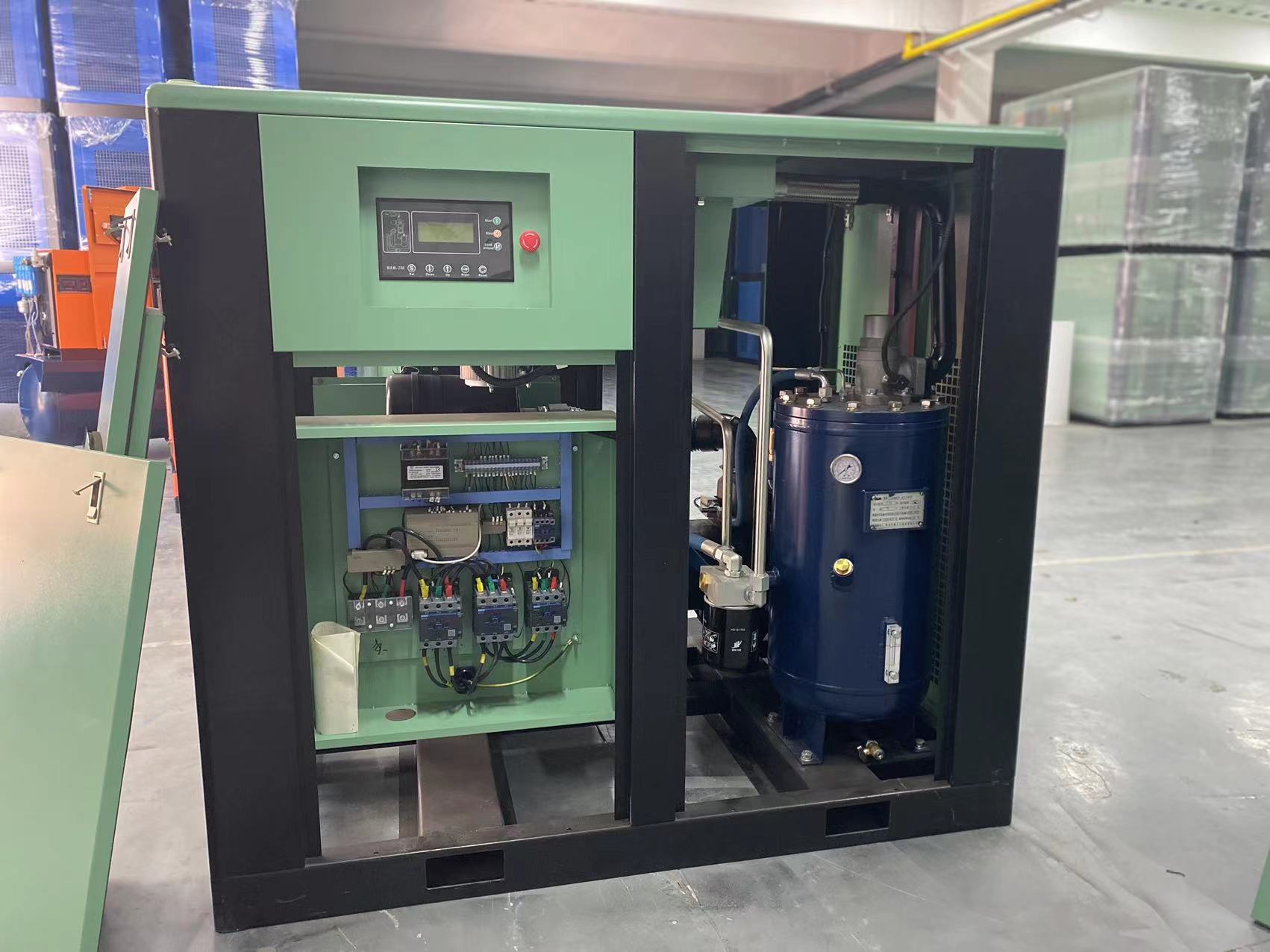
Selecting the perfect fixed-speed rotary screw air compressor involves a careful consideration of various factors. Let's embark on a detailed journey to ensure you make an informed decision tailored to your specific needs.
1. Precise Measurement of Air Requirements
Commence your selection process by accurately assessing your compressed air needs. Measure the volume of compressed air required at the usage point, typically in cubic feet per minute (CFM) or liters per second (L/s). If your operations involve multiple connections, determine if they operate concurrently or intermittently to calculate the total demand accurately.
2. Scrutinize Flow and Pressure Requirements
Delve into the intricacies of your applications by evaluating flow and pressure requirements. Refer to equipment data sheets for individual connections, expressing requirements in pounds per square inch (psi) or bar. Ensure the working pressure of the compressor is 1-2 bar higher than the actual usage pressure, considering pressure drops in the system.
Example: If your highest usage pressure is 8 bar, the compressor's working pressure should be 10 bar.
3. Precision in Compressor Sizing
Navigate the landscape of compressor sizing with precision. Employ comprehensive sizing calculations, incorporating factors such as specific power (kW/CFM), for a nuanced understanding. This guarantees that the chosen fixed-speed rotary screw air compressor aligns seamlessly with the intricate demands of your processes.
Example: A compressor with a specific power of 0.2 kW/CFM means it consumes 0.2 kilowatts of power to produce one cubic foot of compressed air per minute.
4. Integration of Motor Power
Consider the motor power of the compressor, usually measured in kilowatts (kW) or horsepower (HP). Ensure the motor power is sufficient to handle the calculated air demand without being underpowered or excessively oversized.
Example: If your calculated demand is 50 kW, a compressor with a 55 kW motor would be suitable.
5. Efficiency Ratings Matter
Evaluate the efficiency ratings of the compressor. Look for the volumetric efficiency and mechanical efficiency specifications. A higher efficiency rating indicates better overall performance.
Example: A compressor with a volumetric efficiency of 90% means it delivers 90% of the theoretical maximum amount of air.
6. Noise Level Dynamics
Consider the acoustic implications of your compressor choice, especially in noise-sensitive environments. Opt for models with advanced noise reduction mechanisms, and quantify noise levels in decibels (dB).
Example: A compressor with a noise level of 75 dB is quieter than one with 80 dB.
7. Cost of Ownership Analysis
Factor in the total cost of ownership, including initial purchase cost, maintenance expenses, and energy consumption. Often, a slightly higher upfront cost can be justified by lower operating costs over the compressor's lifespan.
Example: Compare the annual energy consumption costs of different models based on local energy prices.
8. Additional Features and Warranty
Explore additional technical features like intuitive control interfaces, advanced safety mechanisms, and user-friendly maintenance protocols. Check warranty terms to ensure long-term support and reliability.
Example: A compressor with a five-year warranty provides added peace of mind.
In Conclusion: A Strategic Fusion of Technical Parameters
The culmination of your fixed-speed rotary screw air compressor selection journey is a strategic fusion of technical specifications with the nuanced demands of your operational landscape. This guide equips you with the knowledge needed to make a judicious decision, ensuring the acquisition of a compressor that stands as an epitome of reliability and operational efficacy.