what is a 2 stage air compressor?
- Share
- publisher
- Leo Wang
- Issue Time
- Dec 28,2023
Summary
In the realm of air compressors, the term "2-stage" denotes a specific design that brings precision and power to compressed air systems. Let's delve into the intricacies of 2-stage air compressors, unraveling the numerical nuances that make them a powerhouse in various industrial applications.
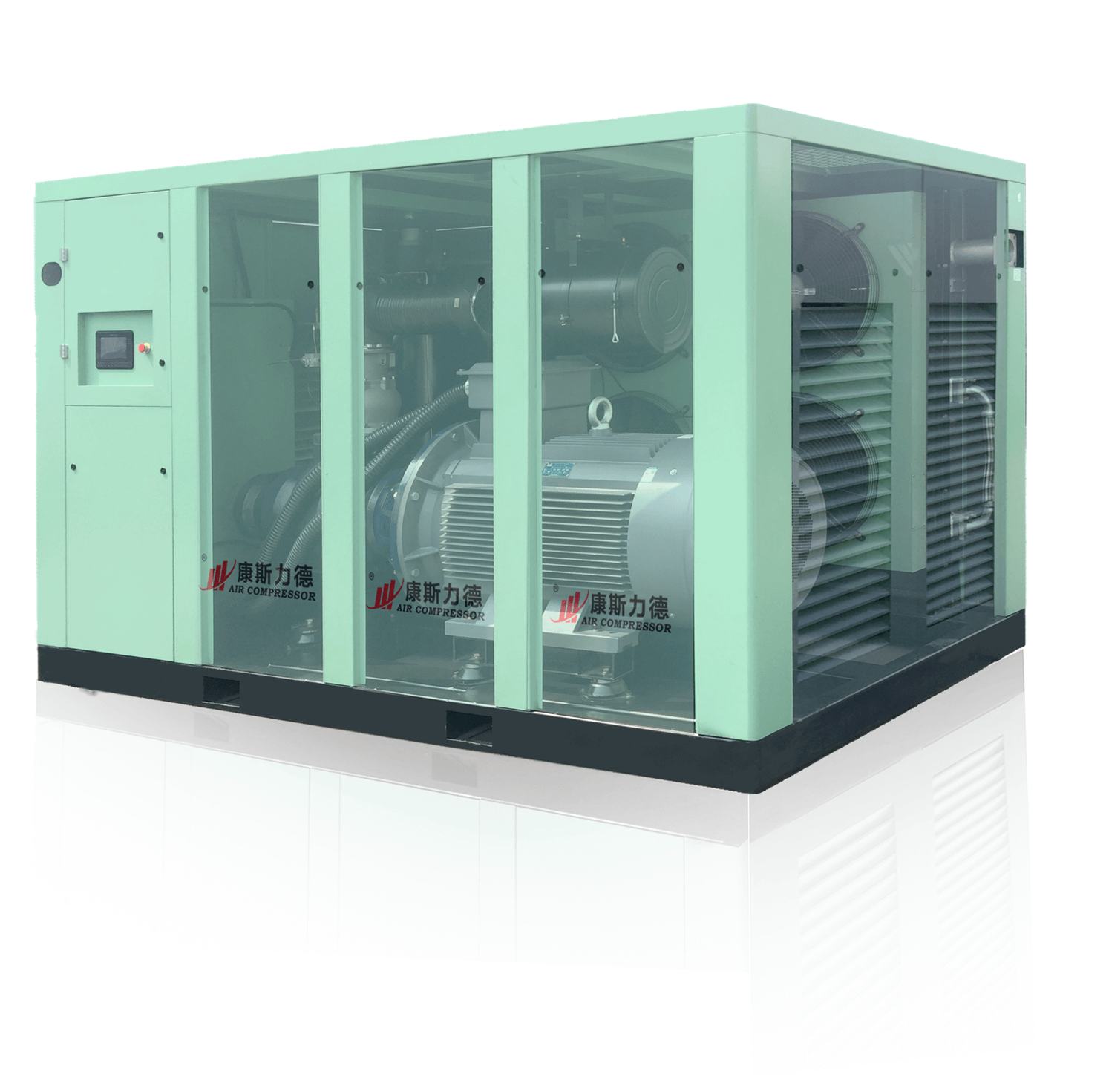
Demystifying 2-Stage Air Compressors: Unleashing Power with Precision
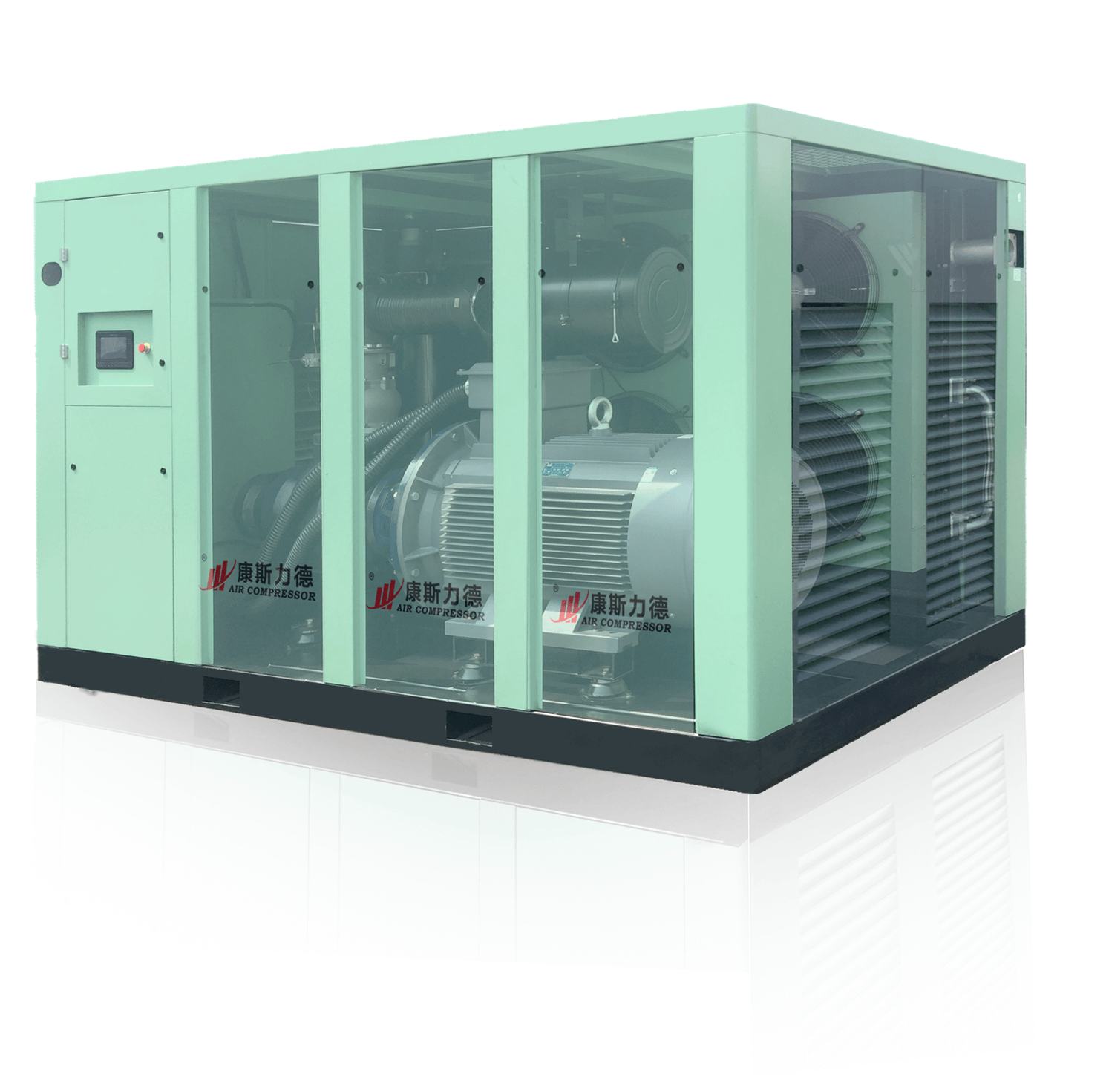
In the realm of air compressors, the term "2-stage" denotes a specific design that brings precision and power to compressed air systems. Let's delve into the intricacies of 2-stage air compressors, unraveling the numerical nuances that make them a powerhouse in various industrial applications.
1. Understanding the Basics:
A 2-stage air compressor, as the name suggests, operates in two stages of compression to achieve higher pressures. Each stage involves a cylinder and a piston, contributing to a seamless and efficient compression process.
2. Pressure Ratio Dynamics:
1. First Stage: The initial compression phase raises the air pressure moderately, typically up to around 50-75 psi (pounds per square inch).
2. Intercooling: Between the stages, there's often an intercooler that cools the air, preventing excessive temperature buildup.
3. Second Stage: The partially compressed air from the first stage enters the second cylinder for further compression. This stage elevates the pressure to the desired level, often ranging from 100 to 250 psi.
3. Advantages of 2-Stage Compression:
1. Higher Efficiency: By dividing the compression process, 2-stage compressors achieve greater efficiency compared to their single-stage counterparts.
2. Lower Heat Output: The intercooling phase mitigates heat, reducing the risk of excessive temperature that could damage components.
3. Suitability for High-Pressure Applications: Ideal for applications demanding higher air pressure, such as in manufacturing, automotive, and certain industrial processes.
4. Numerical Insights:
1. Pressure Output: A 2-stage compressor can deliver pressures ranging from 100 to 250 psi, depending on the specific model and application requirements.
2. Cubic Feet per Minute (CFM): The CFM output varies based on the size and design. Larger compressors can deliver higher CFM, ensuring an ample air supply for demanding applications.
5. Application Scenarios:
1. Automotive Workshops: Ideal for powering pneumatic tools and equipment requiring higher pressures.
2. Industrial Manufacturing: Well-suited for processes like spray painting, where consistent and high-pressure air is essential.
3. Petroleum Refineries: Used for various applications, including valve and instrument control.
6. Maintenance Considerations:
1. Oil Lubrication: Many 2-stage compressors are oil-lubricated, ensuring smoother operation and longevity.
2. Regular Inspection: Periodic checks of components, including valves and intercoolers, are crucial for maintaining optimal performance.
7. Choosing the Right Size:
1. Matching the Application: Consider the specific pressure and CFM requirements of your applications to select the appropriate size.
2. Space Considerations: Evaluate the physical space available for installation, as 2-stage compressors might be bulkier than their single-stage counterparts.
In essence, a 2-stage air compressor is a powerhouse designed for precision and efficiency in scenarios demanding higher air pressures. Understanding its numerical specifications and applications ensures that you harness its capabilities effectively, making it a valuable asset in various industrial settings.