Maintenance instructions for mobile diesel rotary screw truck air compressor
- Share
- publisher
- Leo Wang
- Issue Time
- Feb 26,2023
Summary
1. Check the air filter of the mobile diesel rotary screw truck air compressor every 500 working hours and replace it every 1000 working hours.To prevent air filter clogging and maximize air compressor performance, it is important to inspect the air filter regularly to check for dust, debris and other particles that can reduce the efficiency of the compressor. After changing the air filter, it is recommended to clean the filter housing and check for other signs of damage.
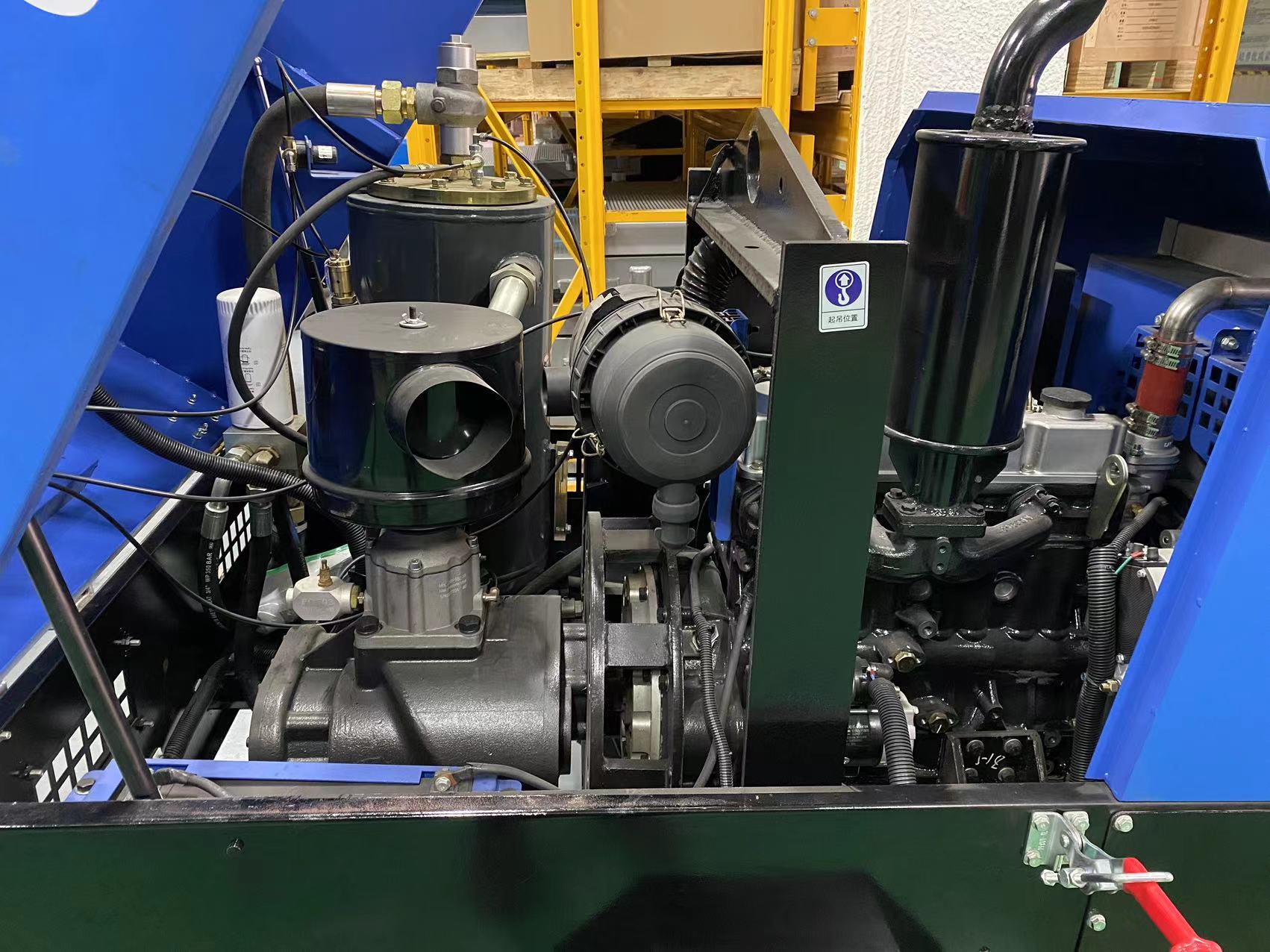
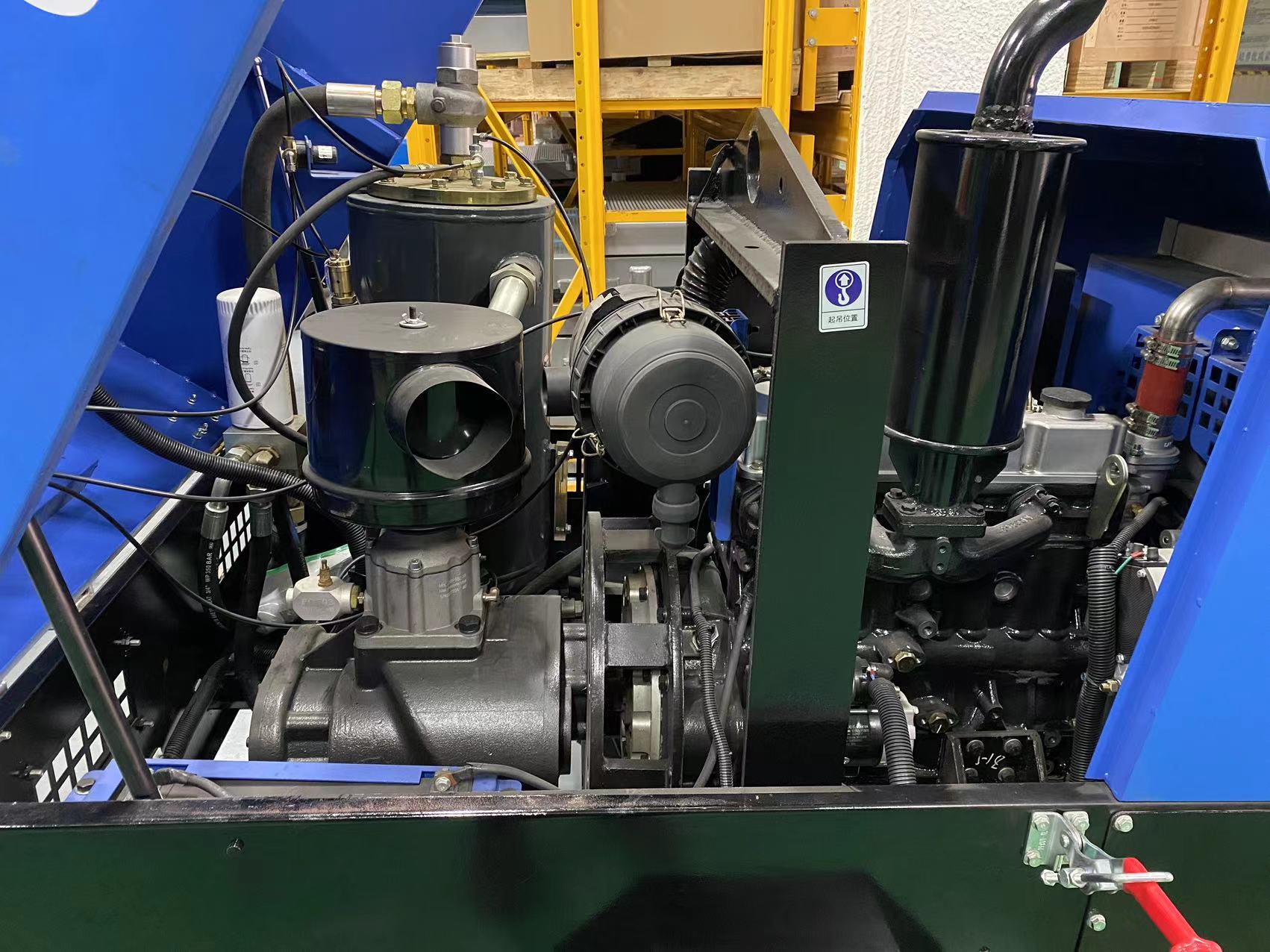
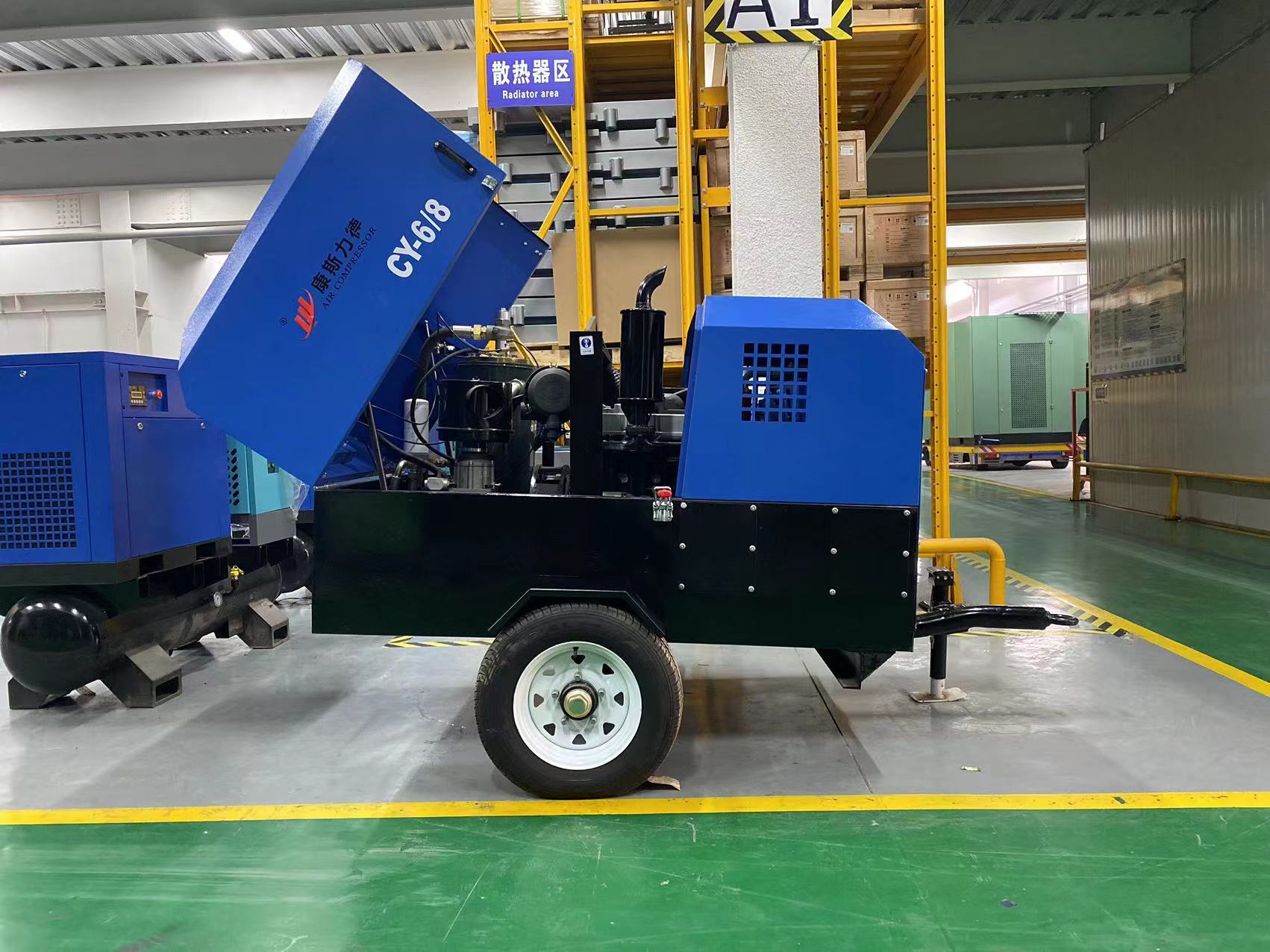
1. Check the air filter of the mobile diesel rotary screw truck air compressor every 500 working hours and replace it every 1000 working hours. To prevent air filter clogging and maximize air compressor performance, it is important to inspect the air filter regularly to check for dust, debris and other particles that can reduce the efficiency of the compressor. After changing the air filter, it is recommended to clean the filter housing and check for other signs of damage.
2. Truck air compressor checks and replace the lubricating oil in the motor and transmission every 1000 working hours. When the oil becomes too dark or has sediment, the lubricating oil should be replaced. This ensures that all moving parts are properly lubricated and that the truck air compressor is functioning properly. Additionally, inspecting the oil level regularly will ensure that it is full to the correct level. Lastly, make sure that the correct type of oil is being used for the compressor.
3. Truck air compressor check the compressor for any oil or fuel leaks and repair them promptly. Compressor leaks can reduce the overall efficiency of the air compressor and can also create a dangerous work environment. Oil or fuel leaks should be addressed immediately to prevent further damage or safety hazards. The leaks should be located and repaired using proper repair kits, seals and replacement parts. Additionally, all bolts, screws, hoses and other components should be inspected regularly to ensure that they are still secure and not damaged.
4. Check the fan belt and adjust tension if needed every 500 working hours. Proper tension on the fan belt will ensure that it is providing enough power to the fan. If the fan belt is too tight or too loose, it can cause wear and tear to the fan and other components. To set the proper tension, most fan belts have an adjustment screw on the back or side of the compressor. The correct tension for the fan belt can usually be found in the truck air compressor's manual. Additionally, it is important to check the fan belt for signs of wear or damage and replace it if necessary.
5. Disconnect the truck air compressor power supply and empty all pressure vessels every 1000 working hours. This procedure should be done to reduce the overall pressure on the truck air compressor and to ensure that there is no moisture or dirt remaining in the pressure vessels. To do this, find the disconnect switch, and turn it off. Once the power is off, the pressure vessels can be vented and emptied. When replacing filters, it is important to remember to replace them with the correct-sized filter and check that they are securely tightened.
6. Change the diesel fuel filter every 500 working hours and keep clean the air filter. The diesel fuel filter is a vital part of the air compressor and should be checked every 500 working hours and changed as necessary. Additionally, it is important to keep the air filter clean and free from dirt and other particles that can reduce the air compressor’s efficiency. Dirt and debris can cause clogging in the compressor, causing the compressor to run less efficiently and even stop working completely.
7. Inspect all piping, hoses and joints for air leaks and tighten them if necessary. Air leaks can be dangerous as they can cause accidental fires or explosions near the compressor. Before operating the compressor, it is important to inspect all the piping, hoses, and joints for any air leaks. If air leaks are found, they should be fixed or replaced as soon as possible. In addition, all fittings and clamps should be tightened securely to prevent further leaks.
8. Inspect the safety shut-off valves and replace them if necessary. Safety shut-off valves are typically located on the back of the air compressor and should be inspected periodically for any signs of wear or malfunctions. If there are any signs of damage, seizing, or corrosion, the valves should be replaced. Additionally, it is important to check that the valves are correctly adjusted and that they are functioning properly.
9. Check the fuel tank, fuel lines, and other components for any visible damage, leakage, or wear and repair or replace as necessary. The truck air compressor’s fuel system can become clogged or damaged after extended use and should be inspected regularly for any wear or damage. Check the fuel and cooling lines for any corrosion, kinks, or blockages and ensure that all lines are secure and free from damage. If any irregularities are found, they should be replaced or repaired as soon as possible.
10. Follow all safety instructions of the manufacturer and keep the area clean and well-ventilated. All instructions pertaining to the operation and maintenance of the compressor should be followed to ensure the safety of the people operating and working with the machine. Additionally, the area should be kept clean and free from any dust and debris that can affect the air compressor’s efficiency. Finally, adequate ventilation should be provided to prevent any buildup of fumes or combustible gases from the compressor.
Jinjing brand reciprocating piston high pressure air compressors are widely used in precision machinery
11kw 0.7/0.8/1.0/1.3mpa Fix Speed screw air compressor For industrial workshops
22KW 0.7mpa-1.3mpa Industrial workshop Stationary Two Stage Saving Energy Screw Air Compressor
Wholesale Industrial Electric Refrigerated Air Freeze Cooling Compressed Dryer for Compressor