How does a screw compressor compress the gas?
- Share
- publisher
- Leo Wang
- Issue Time
- Sep 19,2024
Summary
Screw compressors are widely utilized across various industrial applications for compressing gases with reliability, efficiency, and high performance in mind. Understanding their operation entails exploring its internal mechanics, design principles, operational characteristics and internal operations - this article offers a comprehensive overview of screw compressor working principles - types, mechanisms and efficiency factors which contribute to their effectiveness.
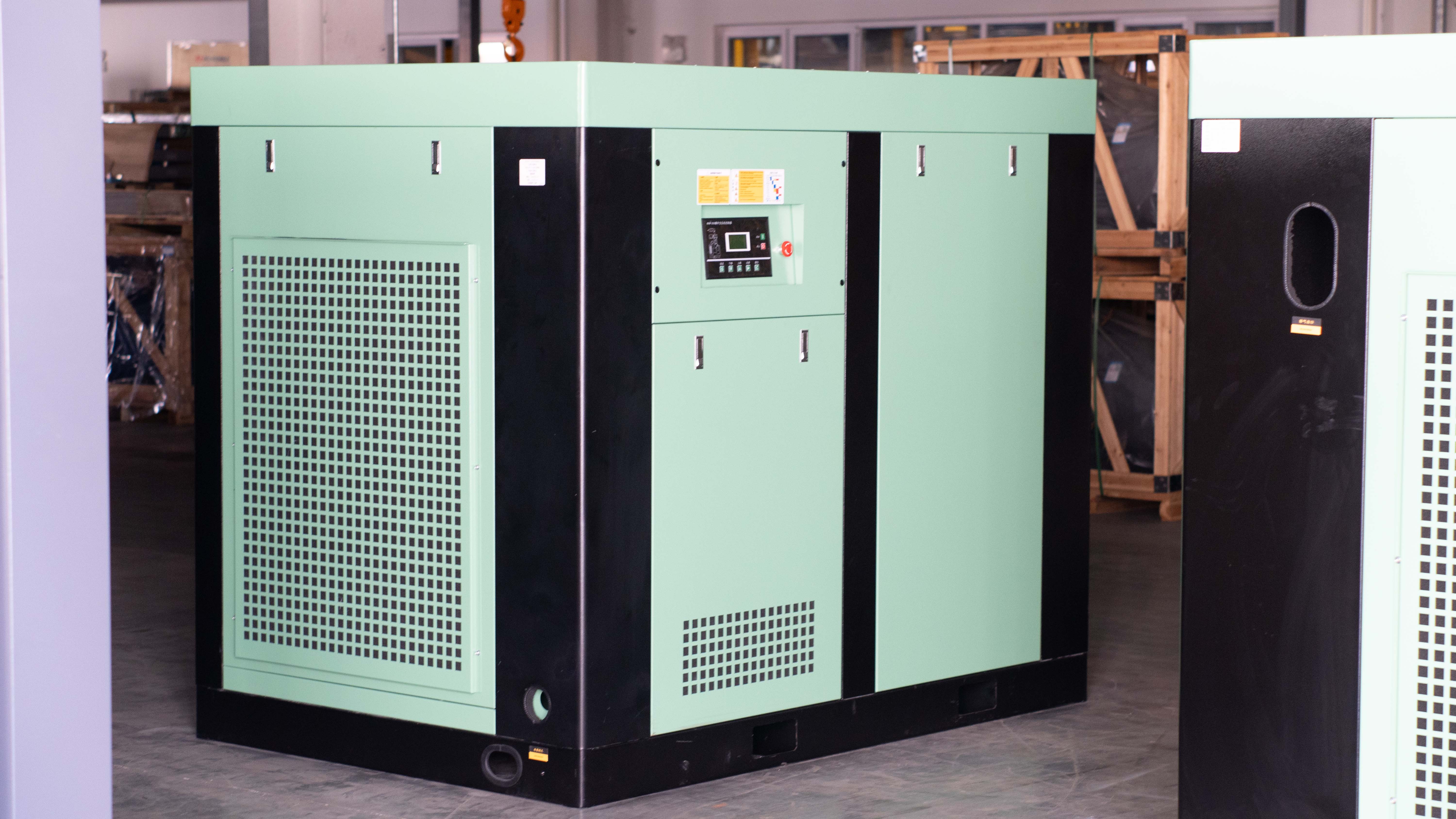
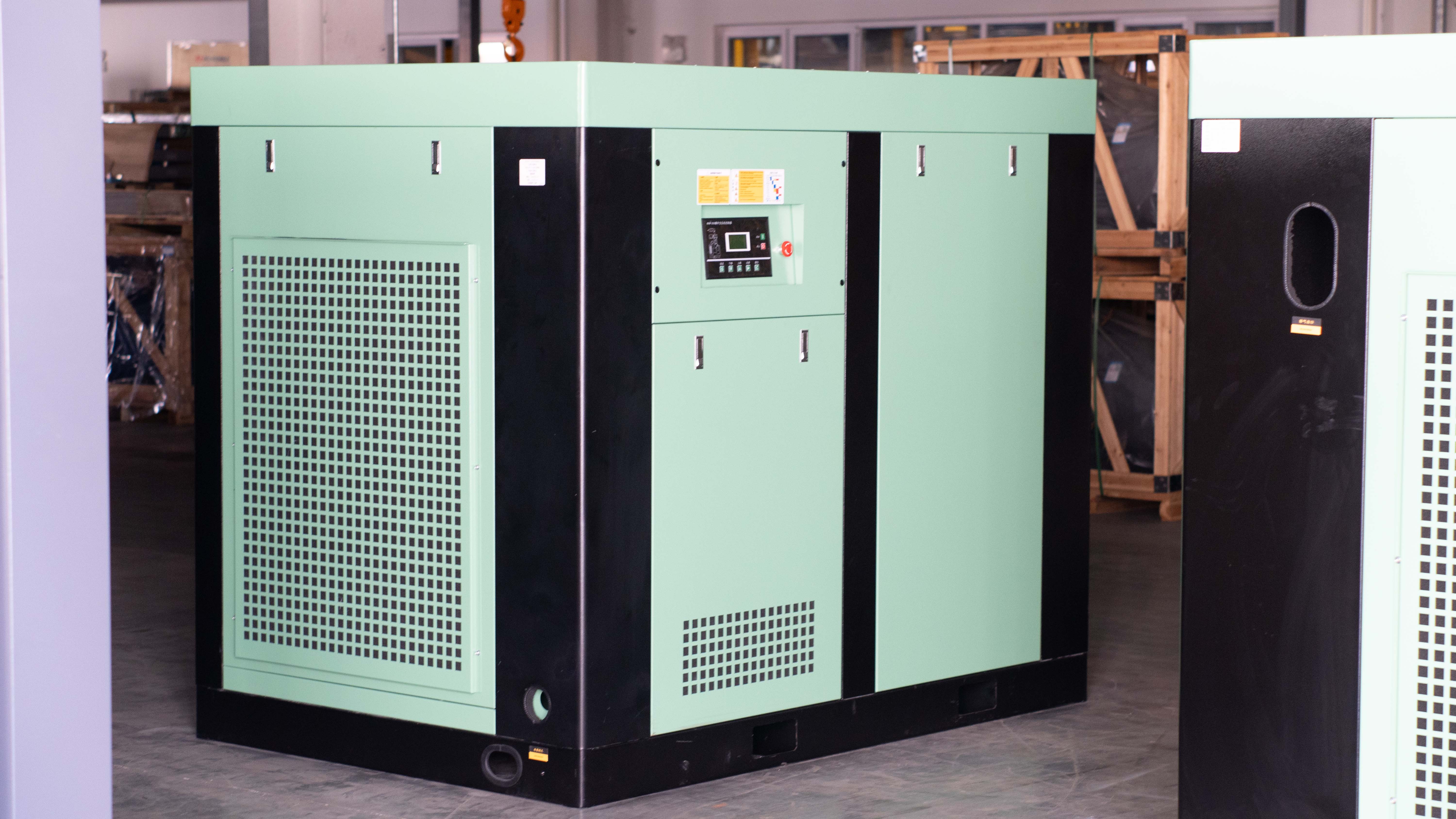
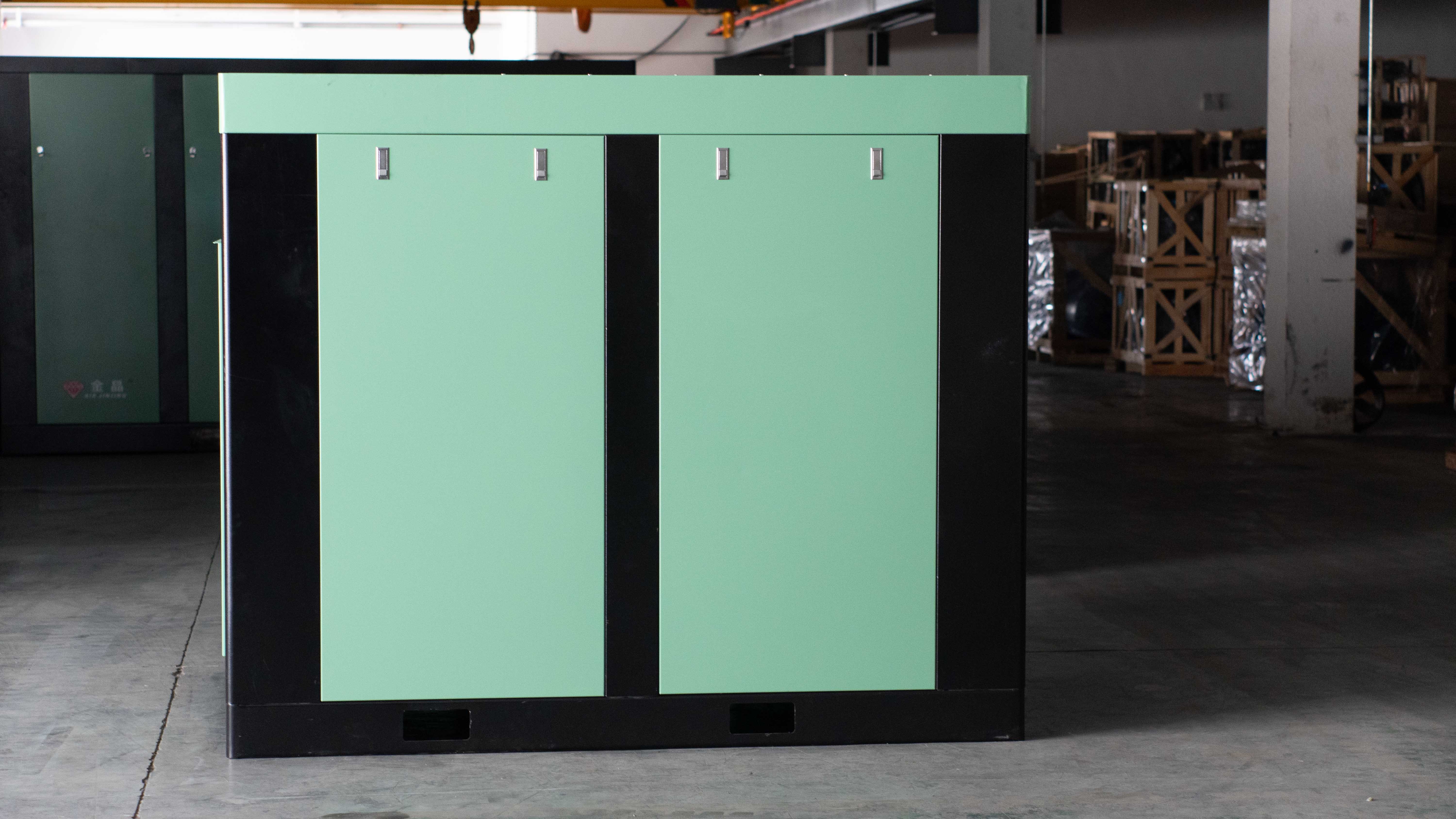
Screw compressors are widely utilized across various industrial applications for compressing gases with reliability, efficiency, and high performance in mind. Understanding their operation entails exploring its internal mechanics, design principles, operational characteristics and internal operations - this article offers a comprehensive overview of screw compressor working principles - types, mechanisms and efficiency factors which contribute to their effectiveness.
Screw Compressors have become an essential tool in today's manufacturing environment. Here is an introduction to screw compressors:
Screw compressors (also referred to as rotary screw compressors) are positive displacement machines used to compress gas using rotating screws. In contrast to reciprocating compressors that rely on pistons for compression, screw compressors rely on rotating elements for their compression action and are therefore well suited for high demand applications such as continuous production lines or distribution hubs.
Different Types of Screw Compressors
Prior to examining compression mechanisms, it's crucial to be familiar with two main types of screw compressors:
1. Oil-Free Screw Compressors:
These compressors utilize air bearings or other techniques to keep oil out of their compressed air supply, making them essential in applications requiring oil-free air, such as food processing, pharmaceuticals and electronics.
2. Oil-Injected Screw Compressors:
These compressors use oil to lubricate and seal rotating screws as well as cool the compressed air, as well as provide cooling properties. They're commonly employed in manufacturing and construction environments where oil presence in the compressed air doesn't present a significant issue.
Compression Process
Screw compressors work by employing two interlocking screws to compress gas. Here is an in-depth overview of how they operate:
1. **Intake**: The compressor draws air or other gases through an intake valve equipped with a filter to capture particulates and contaminants. 2. [Compression]: Once inside, this intake gas enters two rotating screws known as rotors for compression - there are two kinds available (ie, positive displacement and reverse).
- **Male Rotor**: This has a helical shape and is often known as the driving rotor.
Feminine Rotor: This has an complementary helical shape to its male counterpart for optimal functioning.
As the screws rotate, they create pockets between their rotors and compressor casing that trap incoming gas in pockets formed between their rotors, thus decreasing volume while increasing pressure. As these pockets move along the length of each screw's blades during their rotations, trapped gases gradually reduce in volume but increase pressure significantly.
3. Sealing and Cooling**: Oil-injected compressors utilize oil to lubricate their screws, seal gaps between rotors and casing, and cool compressed gas, providing an important sealing action which prevents backflow of compressed air while maintaining compression efficiency without overheating. This sealing action serves to maintain compression efficiency without risk of backflow of compressed air backflow, thus maintaining compression efficiency without risk of overheating.
Screw Compressor Components and Their Applications
1. Rotor(s): These components are responsible for compressing gas and are designed for maximum meshing and compression efficiency. 2. Casing: A housing designed to house and support rotor(s) for safe rotation at high compression pressures.
2. **Bearings**: Bearings provide support to rotating screws and allow for smooth rotation; oil-free models typically use air bearings while oil-injected models use traditional bearings lubricated with compressor oil.
3. Oil Separator**: When installed in oil-injected compressors, this component separates oil from compressed air before discharging, to ensure air quality standards are upheld.
4. **Cooling System**: Components such as oil coolers or intercoolers that dissipate compression heat are integral parts of ensuring optimal compressor performance and longevity.
Energy Factors and Considerations
There are multiple factors that impact a screw compressor's efficiency:
1. Compression Ratio**: This ratio measures the ratio between discharge pressure and intake pressure. An increase in energy usage could result in lower efficiency; optimizing this ratio for specific applications could improve their performance and save costs.
2. **Temperature Management**: For optimal efficiency, effective temperature management is of critical importance. An excess of heat can force compressors to work harder, increasing energy costs and shortening lifespan.
3. Maintenance**: Proper upkeep, such as oil changes, filter replacements and rotor inspections are necessary to ensure efficient operations and avoid higher energy usage and potential breakdowns. Negligence could cause increased energy usage or potential breakdowns.
4. **System Design**: The overall compressed air system design - consisting of pipework and equipment - plays a significant role in its efficiency. Minimizing pressure drops and optimizing airflow are proven methods for improving performance.
5. **Load Management**: Utilizing variable-speed drives (VSD), compressors can adjust their speed according to demand, saving energy when demand falls off during low demand periods.
Screw Compressors Offer Advantages in Compression Systems
1. Continuous Operation**: Screw compressors offer a consistent and continuous supply of compressed air for applications requiring constant pressure and volume.
2. **High Efficiency**: Screw compressors tend to offer superior efficiency and lower specific power consumption than reciprocating compressors, with their smaller moving parts and robust designs contributing to their high degree of reliability and durability.
3. [Reliability and Durability]: These characteristics contribute to screw compressors' dependability and durability over their reciprocating counterparts.
4. Reduced Noise Levels**: Screw compressors typically operate more quietly than their reciprocating compressor counterparts, making them ideal for noise-sensitive environments.
5. Flexible Output**: Variable speed screw compressors offer flexible output to match fluctuating demand, providing improved energy efficiency.
Applications of Screw Compressors
Screw compressors can be found in many applications, including:
1. Production**: Powering pneumatic tools, automation systems and machinery with compressed air. 2. Construction: Supplying tools and equipment on construction sites with compressed air for use at sites. 3. HVACC Systems: Delivering compressed air for various components within their HVAC systems.
2. **Automotive**: Utilizing oil-free air for tire inflation, paint spraying and engine testing tasks. 5. [Food and Beverage]: Employing applications requiring oil-free air in order to ensure product quality and safety.
Conclusion
Understanding how screw compressors operate offers valuable insights into their operation, efficiency, and applications. By harnessing screw compression principles to produce reliable compressed air solutions that reduce energy usage. Routine maintenance checks, effective system designs and cooling are critical elements to maximize performance while decreasing energy consumption. Screw compressors continue to play an essential role across various industrial sectors with continuous operations providing continuous high efficiencies with reliability as the key benefits.
1. The original airend is sourced directly from Germany, ensuring top-notch engineering and quality.
2. The air produced is 100% oil-free and is certified by the renowned German organization TUV, ensuring the highest standards of purity.
3. Equipped with a centrifugal fan, this system offers a superior cooling effect, maintaining optimal performance and efficiency.
The JINJING brand of 55 KW rotary screw air compressors is an ideal choice for industrial and commercial applications.
75 KW 100 HP Mobile Diesel Rotary Screw Truck Air Compressor 100 cfm 7/8/10/13 Bar Equipment Leasing
1. Compact and portable: The compact and portable design of the Jinjing brand diesel rotary screw air compressor for truck make
Jinjing brand reciprocating piston high pressure air compressors are widely used in precision machinery