Which is better, reciprocating or rotary compressor?
- Share
- publisher
- Leo Wang
- Issue Time
- Sep 28,2024
Summary
Air compressors are indispensable pieces of equipment in many industries, powering pneumatic tools, machinery and processes with pneumatic power. Selecting the appropriate air compressor type is key for optimizing performance, efficiency and cost-effectiveness of any application; two common types are reciprocating compressors and rotary compressors
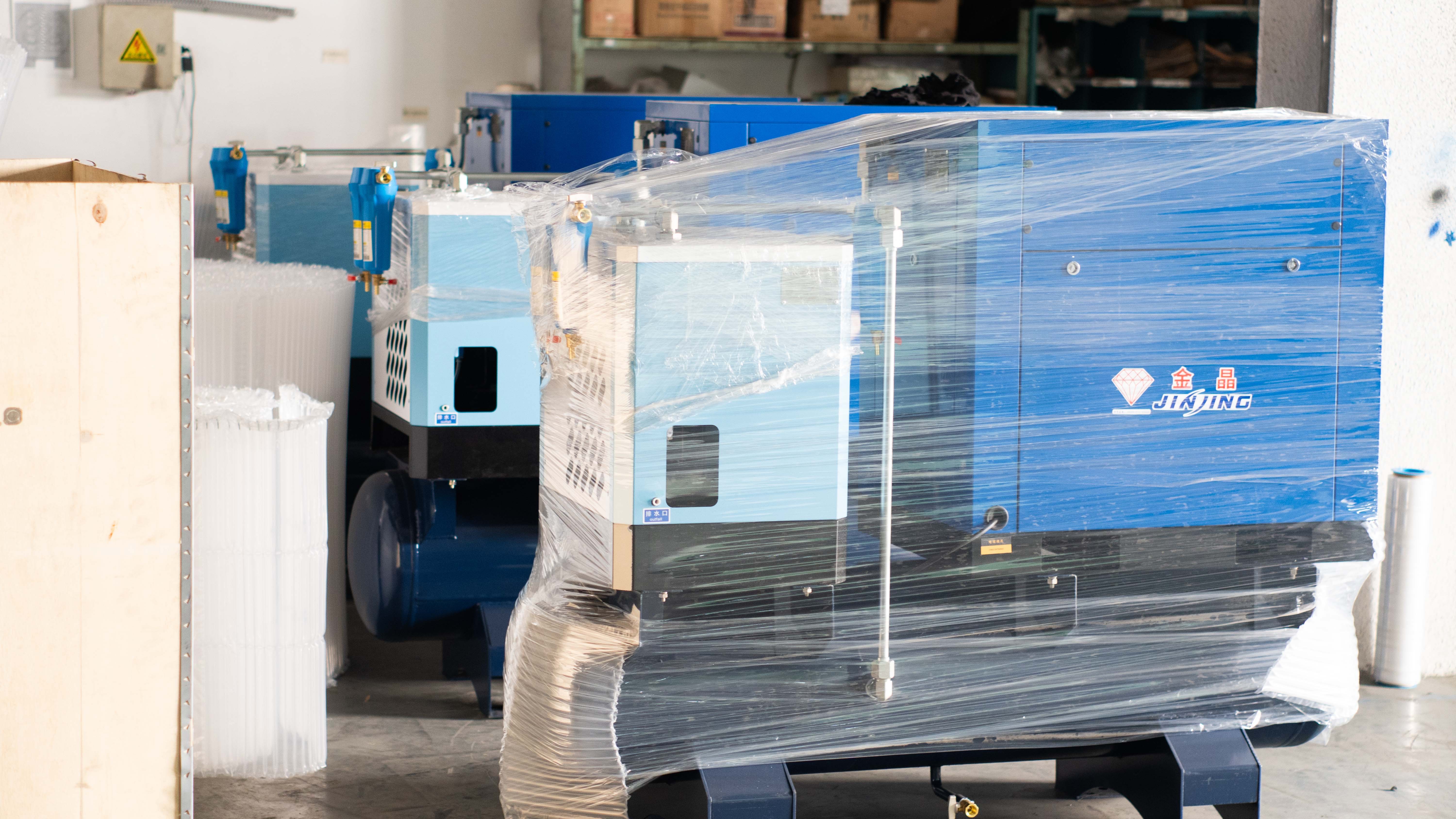
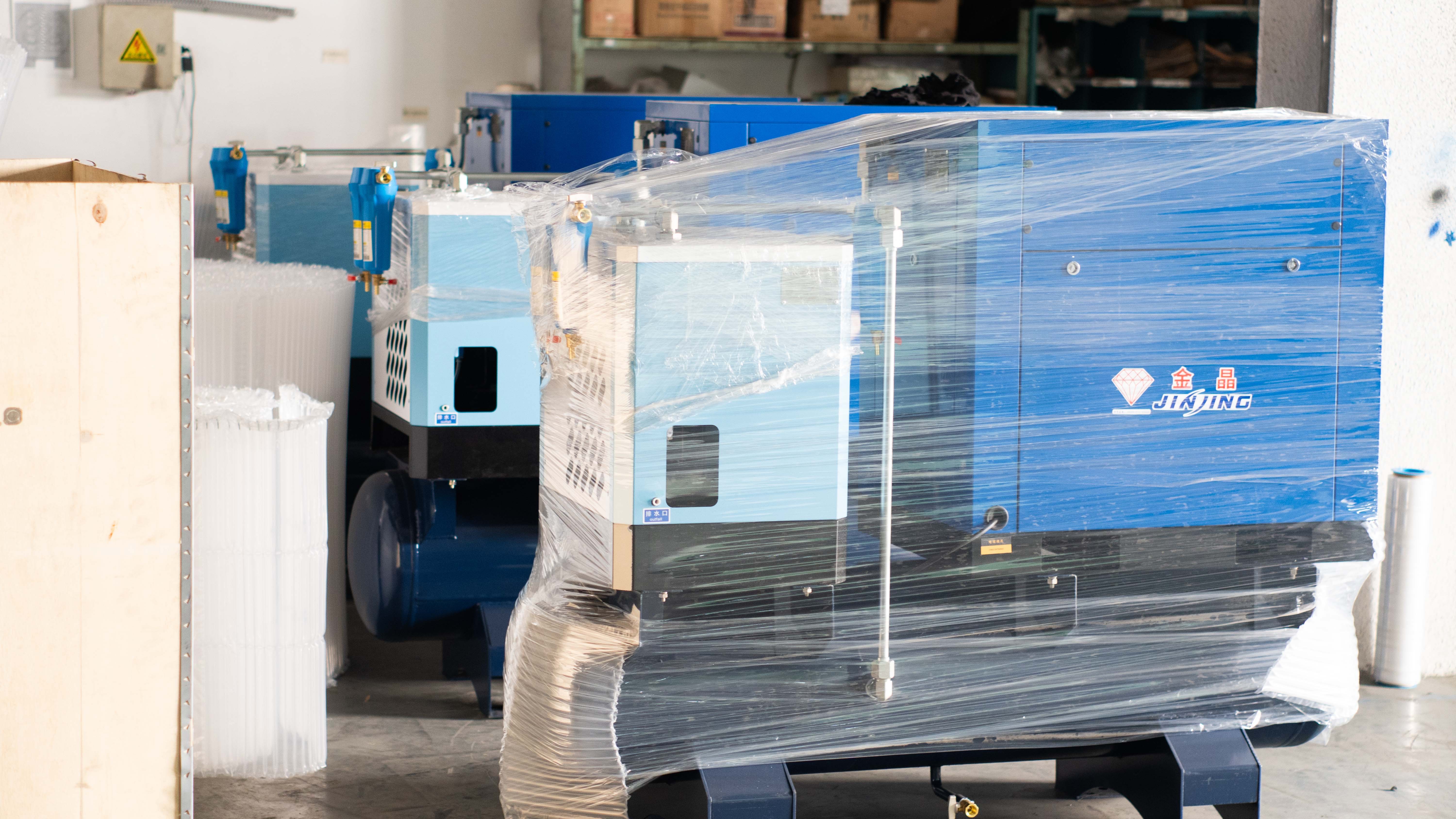
Air compressors are indispensable pieces of equipment in many industries, powering pneumatic tools, machinery and processes with pneumatic power. Selecting the appropriate air compressor type is key for optimizing performance, efficiency and cost-effectiveness of any application; two common types are reciprocating compressors and rotary compressors - we will compare both types in depth here highlighting their advantages, disadvantages and suitable applications so that you can make an informed decision as to which fits best your needs.
1. Introduction and Importance of Air Compressors for Sophisticated Machines (Air Compressors)
Air compressors are indispensable tools in industries like manufacturing, automotive, food and beverage production, oil & gas exploration & extraction and pharmaceuticals. Air compressors convert power (from an electric motor or gasoline/diesel engine) into potential energy stored as pressurized air for later use - whether this means powering pneumatic tools, packaging equipment conveyor belts paint sprayers or much else!
Introduction to Reciprocating and Rotary Compressors
Reciprocating and rotary compressors each have unique working principles, advantages, and drawbacks that may make them suitable for certain applications. Understanding these differences between them is crucial in selecting equipment suitable to your specific needs.
Reciprocating Compressors (RCP)
Working Principle
Reciprocating compressors (also referred to as piston compressors) use a piston in a cylinder to compress air. As it moves downwards, it draws in air through an inlet valve; and as it returns upwards it compresses it and forces it through a discharge valve into storage tanks - repeating this cycle and compressing an equal volume each time.
Benefits of Reciprocating Compressors
1. High Pressure Output**: Reciprocating compressors have the capability of producing high pressure output (up to 30,000 psi), making them ideal for applications requiring high-pressure air such as in the oil and gas industry.
2. **Affordability**: Reciprocating compressors often offer lower initial costs compared to their rotary counterparts, making them an economical solution for small-scale applications.
3. Efficiency at Intermittent Operation**: These machines are very effective for intermittent operations with fluctuating demand for compressed air, such as intermittent work at construction sites or intermittent operations by hotels and hospitals. 4. Variety of Configurations**: Offering single and multi-stage configuration options that provide flexibility to meet different pressure requirements, there is something suitable here for nearly every need.
Reciprocating Compressors Have Some Drawbacks as Well
1. Noise and Vibration:
Reciprocating compressors tend to produce greater noise levels and vibration due to piston movement, with noise levels often reaching 85dB in industrial settings requiring additional noise control measures.
2. Maintenance Requirements:
Due to their complex design and high number of moving parts, reciprocating compressors require regular maintenance including lubrication and inspection of pistons and cylinders as well as replacing worn-out components.
3. Limited Continuous Operation:
They may be unsuitable for continuous duty cycles as they may become overheated when exposed to extended heat without adequate cooling measures in place.
Applications of Reciprocating Compressors
Reciprocating compressors are well-suited to applications that require high pressure but are intermittent in nature, such as:
Automotive workshops, construction sites, small manufacturing units and oil and gas industries for well drilling and extraction processes.
Rotary Compressors Working Principle
Rotary compressors employ various compression mechanisms involving rotating elements like screws, vanes or scrolls. The most widely-used type is the **rotary screw compressor** which utilizes two helical screws rotating in opposite directions - trapping air between their gaps as it travels from intake side to discharge side for compression.
Advantages of Rotary Compressors
1. **Continuous Operational Capability**: Rotary compressors are engineered for continuous operation, making them suitable for industries with a steady air demand. They offer reliable performance without overheating during long runs without creating too much heat build-up in their systems. This makes rotary compressors perfect for industries requiring constant air supply.
2. **Low Noise Levels**: Due to their rotary movement and lack of reciprocating parts, rotary compressors tend to produce lower sound levels (around 60-75dB), creating a quieter working environment.
3. **Reduced Maintenance**: Since less moving parts require fewer repairs and wear-and-tear, maintenance requirements for rotary screw compressors tend to be reduced significantly - oil changes and filter replacement are the only scheduled services required of them.
4. **Energetic Efficiency**: Rotary compressors are highly energy-efficient, especially those equipped with variable speed drive (VSD) models that adjust motor speed based on air demand - potentially cutting energy consumption by up to 35%.
Rotary Compressors Have Certain Drawbacks
1.**Larger Initial Cost**: Rotary compressors typically have higher initial costs compared to reciprocating compressors, which could present challenges to small businesses or workshops.
2. **Complexity**: Rotary compressors' mechanical complexity requires expert knowledge for repairs and maintenance.
3. **Limited Pressure Range**: Rotary compressors do not support applications requiring extremely high pressures; typically operating up to 150 psi is their operating range.
Rotary Compressors Are Ideal Solutions for Applications that Require High Flow Volume Capacity
Rotary compressors are ideal for applications that require constant air supply, such as:
Large-Scale Manufacturing | Food and Beverage Production, Pharmaceutical Industries, Chemical Plants and Power Generation: Four Way Comparison
### Efficiency on Reciprocating Compressors**: Continuous applications often suffer lower efficiency due to frequent starting and stopping which results in energy losses as well as overheating issues.
Noise Levels
mes mes - Reciprocating Compressors will produce greater noise levels (85-95dB), necessitating noise-reduction enclosures.
mes mes mes mes Rotary Compressors offer lower noise emissions with reduced 60 to 75dB making them suitable for indoor environments and environments with noise restrictions due to piston movement requiring noise-reducing enclosures.
Maintenance Requirements for Air Purifiers (### Maintenance Needs for A/C Systems (## Maintenance Requirements for AC Units (10) )
Reciprocating Compressors require more maintenance due to multiple moving parts that need frequent lubrication and component replacements; whilst Rotary Compressors typically only need oil and filter changes.
### Initial Cost and Operating Cost (ICC)
Reciprocating Compressors offer lower initial costs but potentially higher operating expenses due to ineffective efficiency and more frequent maintenance needs.Teatrul Rotary Compressors typically require greater investments initially but over time can result in lower operational expenses due to better efficiency and reduced maintenance needs.
Air Quality
Reciprocating Compressors may release oil contaminants into the air stream; oil-free models are available but come at a higher price point. mes Rotary Compressors tend to offer higher air quality with reduced carryover, especially oil-free rotary screw models.
1. How to Select an Appropriate Compressor
### Factors to Keep in Mind Its mes mes chaudiere requirements of your application and required pressure levels accordingly.
two to Consider 3 Noise Tolerance should also be evaluated along with noise reduction measures that might be required in this regard.
4. Assess Maintenance Capabilities Evaluate availability of maintenance personnel and parts. 5. Review Initial and Operating Costs Analyze budget constraints considering both upfront and long-term costs.
Industry-Specific Needs and Prerequisites for Compliance Testing Services
Manufacturing environments tend to favor rotary compressors due to their continuous operation and reduced noise level, while automotive applications favor reciprocating compressors for their high pressure output and cost effectiveness.
Food and Beverage Industries: Rotary compressors are preferred due to their ability to provide higher air quality while operating without interruption.
#6. Conclusion Both reciprocating and rotary compressors each possess unique advantages and disadvantages, with reciprocating compressors excelling at applications requiring high pressure with intermittent use, while rotary compressors tend to excel at continuous operation environments with stable air demands and reduced noise levels. The choice ultimately comes down to individual application requirements regarding efficiency, noise level, maintenance needs, costs of ownership or cost considerations - by understanding key differences and factors affecting this decision, industries can select an ideal compressor that maximizes performance, efficiency and cost-effectiveness.
1. The original airend is sourced directly from Germany, ensuring top-notch engineering and quality.
2. The air produced is 100% oil-free and is certified by the renowned German organization TUV, ensuring the highest standards of purity.
3. Equipped with a centrifugal fan, this system offers a superior cooling effect, maintaining optimal performance and efficiency.
75 KW 100 HP Mobile Diesel Rotary Screw Truck Air Compressor 100 cfm 7/8/10/13 Bar Equipment Leasing
1. Compact and portable: The compact and portable design of the Jinjing brand diesel rotary screw air compressor for truck make
Jinjing brand reciprocating piston high pressure air compressors are widely used in precision machinery
11kw 0.7/0.8/1.0/1.3mpa Fix Speed screw air compressor For industrial workshops