What are the different types of compressors?
- Share
- publisher
- Leo Wang
- Issue Time
- Oct 12,2024
Summary
Compressors are essential components in many industries, from powering pneumatic tools to supporting refrigeration cycles. Simply defined, a compressor is a machine which increases gas pressure by decreasing its volume. Compressors play an essential role across industries including manufacturing, automotive, chemical processing and HVAC systems. Understanding their unique uses is crucial in selecting the proper compressor equipment.
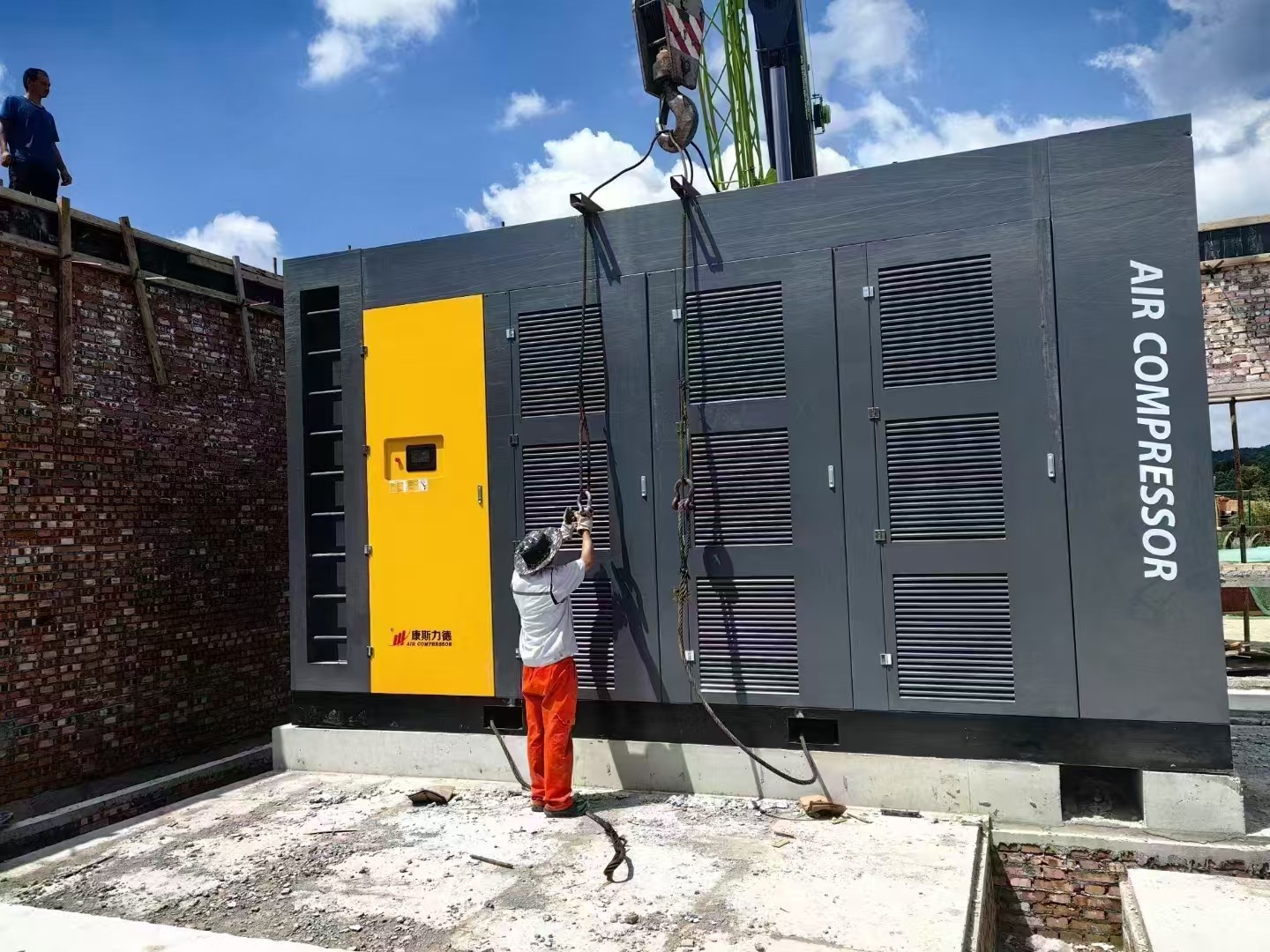
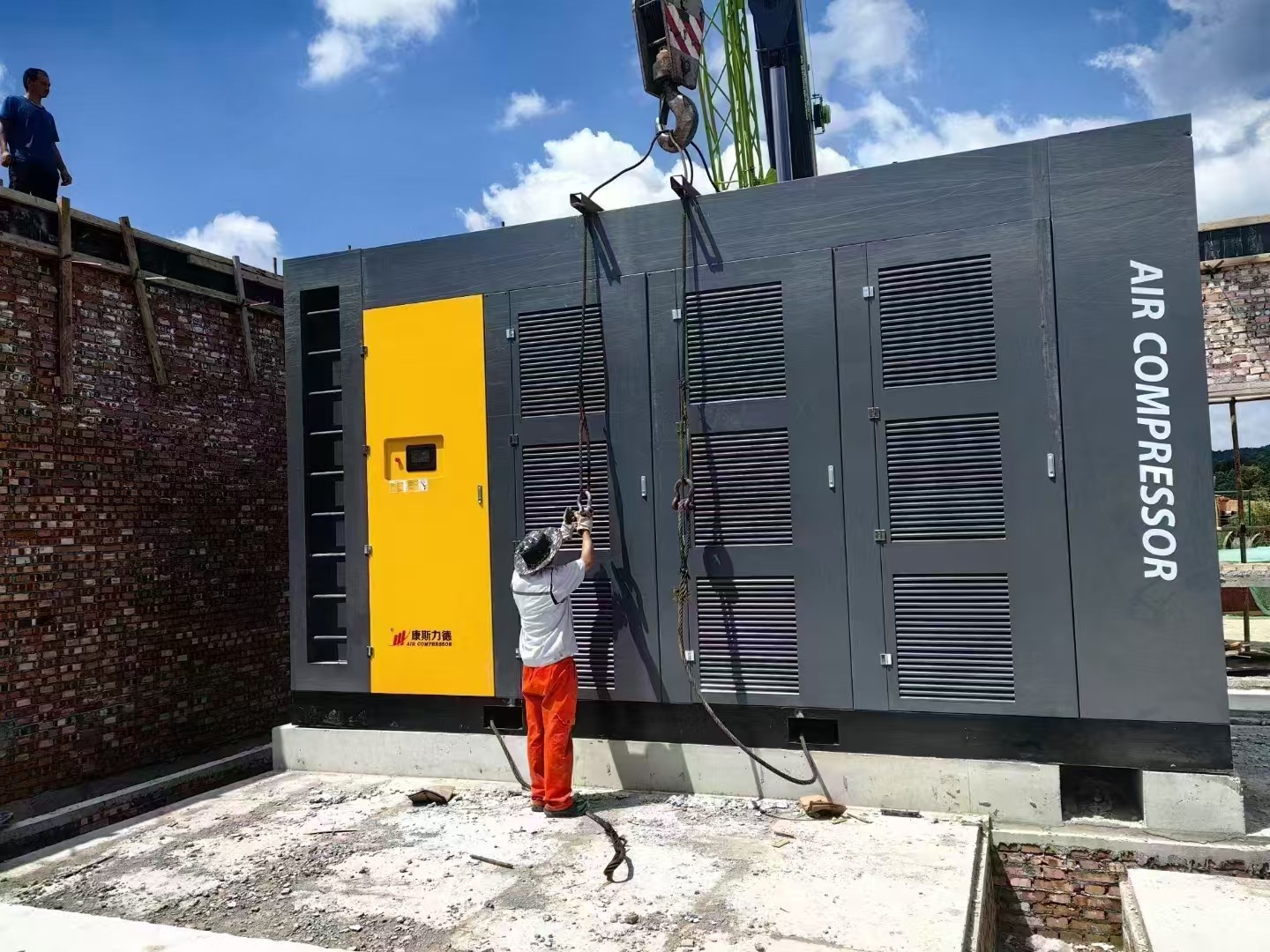
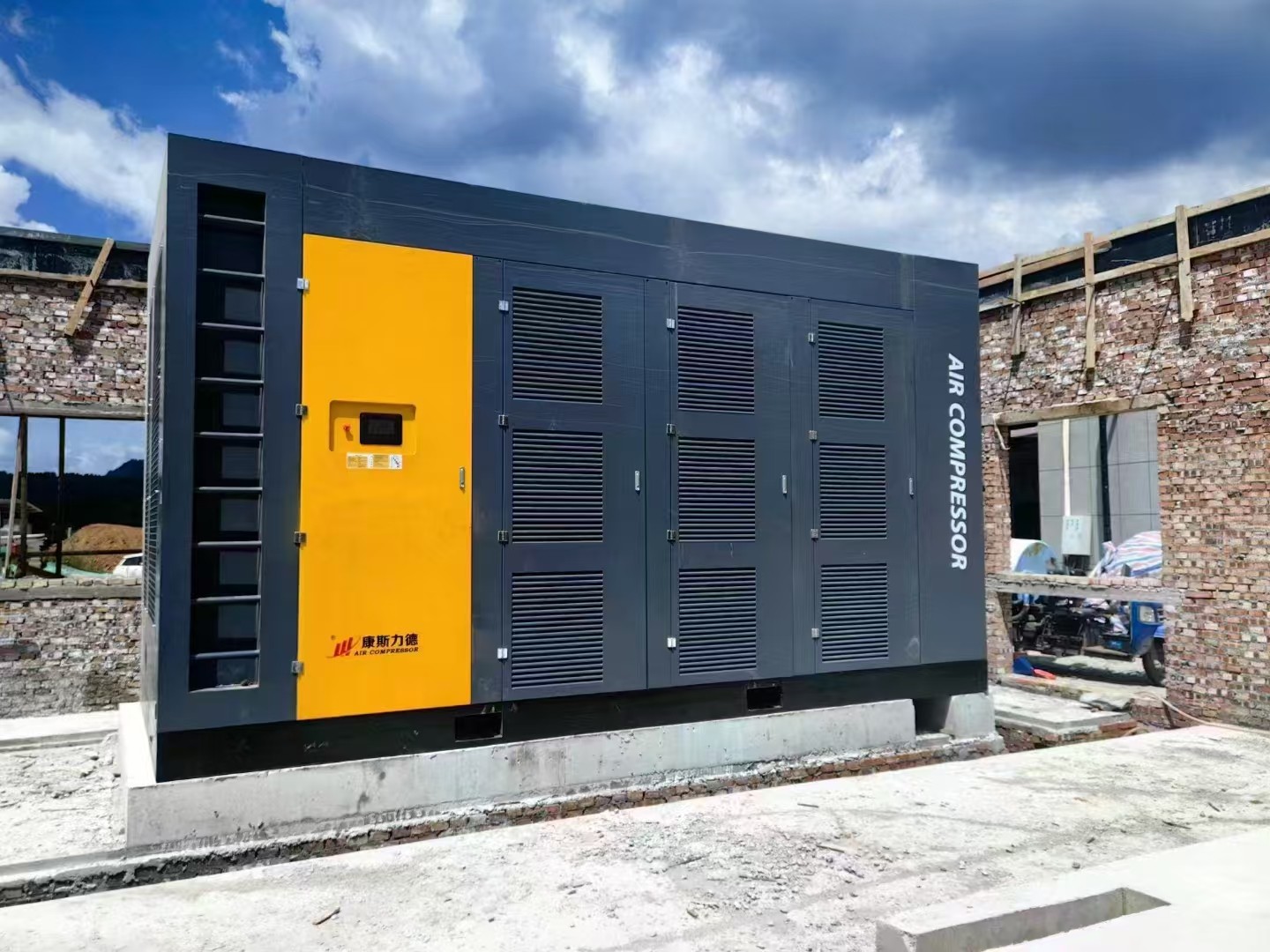
Compressors are essential components in many industries, from powering pneumatic tools to supporting refrigeration cycles. Simply defined, a compressor is a machine which increases gas pressure by decreasing its volume. Compressors play an essential role across industries including manufacturing, automotive, chemical processing and HVAC systems. Understanding their unique uses is crucial in selecting the proper compressor equipment. This article offers an in-depth review of various types of compressors, such as reciprocating compressors, rotary compressors, centrifugal compressors and axial compressors; as well as offering advice for choosing one based on your individual requirements.
Reciprocating Compressors
Reciprocating compressors, also referred to as positive displacement compressors, are widely utilized in applications requiring high pressure but relatively low flow rates. Their unique design works by trapping an exact volume of gas in their compression chamber before compressing and then decreasing it through reciprocation motion.
2.1 Piston Compressors
**Piston compressors** are the most prevalent form of reciprocating compressor, operating much like an internal combustion engine. A piston powered by a crankshaft compresses air or gas in an enclosed cylinder to compress its contents.
Working Principle**: In the intake stroke, the piston moves downward to draw in gas from an intake valve. On compression stroke, however, the piston moves upward to compress it before being released out through an exhaust valve.
Applications: Piston compressors are ideal for high-pressure applications, including pneumatic tools, air brakes and refrigeration systems.
- **Efficiency**: These compressors are known for their superior efficiency at lower flow rates, yet at higher flow rates can become less efficient due to mechanical losses and heat production.
Example: An industrial piston compressor typically offers pressures up to 30 MPa (300 bar), making it suitable for demanding applications such as natural gas processing.
Diaphragm Compressors (DC Compressors)
Diaphragm compressors are a type of reciprocating compressors which use a diaphragm instead of piston to compress gas in their chamber. By applying hydraulic or mechanical pressure on this diaphragm, it compresses the chamber's contents and compresses gas more effectively.
Working Principle: A diaphragm seal forms to keep compressed gas away from mechanical parts and reduce contamination risk, making this ideal for compressing toxic or hazardous gases in chemical and pharmaceutical industries. [Applications]: Ideal for compressing toxic or hazardous gases when compression rates need to remain at an absolute minimum.
Advantages of Hermetic Compressors
These compressors offer high purity of compressed gas due to hermetic separation of gas and oil. * Efficiency These are highly efficient compressors for applications requiring gas purity, safety, or security but may have reduced capacities when compared with piston compressors.
Rotary Compressors *Rotary Compressors** are one of the main categories of compressors which use rotating elements to compress gases, typically used in applications requiring continuous air supply and higher flow rates.
Screw compressors use two interlocking helical rotors (screws) to compress gas as it travels along their lengths, compressing as it goes.
Working Principle: As the screws turn, gas is drawn into the machine by its rotating screws, trapped between rotors and compressed as it travels towards its discharge end. Applications: Compressed air compression systems can be found widely throughout manufacturing, mining and construction industries where continuous airflow is essential.
Advantages of Screw Compressors
Advantages include high reliability, reduced noise levels and less maintenance as there are fewer moving parts involved. *Efficiency*: Screw compressors offer efficient performance across a range of flow rates making them the ideal solution for medium to large-scale industrial applications.
Example: A large screw compressor can deliver up to 500 cubic meters per hour at 15 bar pressure, making it suitable for heavy-duty applications.
Scroll Compressors (Fig 3.2)
Scroll compressors consist of two interleaved spiral scrolls, one stationary and the other orbital, that compress gas by following an orbiting path.
Working Principle: As the orbiting scroll moves, gas pockets form, compress, and then decompress as part of its continuous motion, producing a continuous and pulse-free supply of compressed air.
Applications of these motors include HVAC, refrigeration and small to medium industrial applications.tarii They boast low noise, vibration levels and compact size - three advantages that make these units particularly appealing.
Scroll compressors are highly effective at meeting moderate pressure needs with continuous operation. A typical application would include air conditioning systems with capacities between 2-60 tons.
3.3 Vane Compressors
Vane compressors, also referred to as **rotary vane compressors**, employ a rotating rotor with multiple vanes that slide in and out to compress gas inside a housing.
Working Principle: As the rotor spins, centrifugal force pushes outward on its vanes to trap and compress gas against housing walls, trapping and compressing gas within.
Applications: Common in automotive, food packaging and printing industries.
Advantages of Oil Free Compressors
efficacite chaudiere chaudiere is ideal for simple, reliable, and consistent performance applications with specific niche applications in mind. It offers simple operation while being reliable over long runs of time and offering moderate efficiency compared to both screw and scroll compressors but highly effective nonetheless.
1. Centrifugal Compressors
Centrifugal compressors are dynamic compressors that use a rotating impeller to transfer energy from rotating wheels onto gas molecules, which then transforms to pressure as the flow passes through a diffuser.
Working Principle: Gas enters the center of a rotating impeller, which accelerates it toward a diffuser where its kinetic energy can be converted to pressure.
Applications include high-volume petrochemical processing, power generation and HVAC systems in large buildings. Its Vorteile include higher flow rates with relatively reduced maintenance due to fewer moving parts.
- Efficiency: Centrifugal compressors are highly efficient at high flow rates but may lose efficiency at lower flow rates.
For instance, centrifugal compressors can deliver up to 60,000 cubic meters per hour at pressures between 3-20 bar.
1. Axial Compressors
Axial compressors are dynamic compressors that compress gas by accelerating it axially along a series of rotating and stationary blades, compressing it as it passes.
Working Principle of Compressor: Gas flows along the axis of the compressor and through multiple stages of rotating blades (rotors) and stationary blades (stators), compressing it stage by stage.
Applications: Commonly found in jet engines, gas turbines and industrial processes that require very high flow rates.Advantages: Able to produce high flow rates while taking up minimal space on site.
- Efficiency: Highly effective for large-scale applications that demand continuous high flow rates, such as jet engines. For example, Axial compressors in jet engines can achieve pressures up to 40 bar with flow rates exceeding 100,000 cubic meters per hour (m3/h).
Compare Compressor Types
### Advantages and Disadvantages of 3D Printing Technology
| Compressor Type | Advantages | Disadvantages |
|
Reciprocating | High pressure, wide variety of applications | Noisy with required maintenance | Rotor Screw | Continuous flow with lower noise output but higher initial costs and cooling system requirements |
Scroll | A compact, quiet, low maintenance solution limited to lower capacities | | Centrifugal | High flow rates with minimal maintenance costs | Reduced efficiency at lower flows | | Axial | Extremely high flow rates with excellent efficiency for large applications | Complex design costs and costs are typically involved |
Applications ###6.2 (Forestry Industry Applications)
Reciprocating Compressors**: Perfect for applications requiring high pressure at low to moderate flow rates, such as pneumatic tools and small-scale refrigeration.
Rotary Screw Compressors**: Great for medium to large-scale industrial uses that need consistent air supply.
- **Scroll Compressors** are ideal for HVAC systems and small industrial processes requiring low noise levels and compact designs, while centrifugal compressors offer maximum efficiency when applied to high-flow applications like chemical processing or large building HVAC systems.
- **Axial Compressors**: These compressors are crucial in high-flow, high-pressure applications like jet engines and power generation.
1. Tips to Consider When Selecting the Appropriate Compressor
Selecting the ideal compressor requires taking into account several key factors:
- Calculate Your Flow Rate and Pressure Needs**: Determine the required capacity (in m3/h) and pressure (in bar or psi).
Application and Industry Needs**: Different industries have various needs. For instance, chemical firms might prioritize gas purity while automotive industries might need high-pressure air.
Initial and Operating Costs**: Consider both initial purchase price and long-term operational expenses such as energy consumption and maintenance.
energetique Efficiency: Choose compressors with higher energy efficiency ratings when used continuously.
Maintenance Requirements**: Some compressors require more frequent maintenance, which could impact costs and downtime.
Understanding the various types of compressors and their applications is vital to making an informed decision about them. From reciprocating compressors used for high pressure applications to centrifugal compressors used in large scale industrial processes, each type offers its own set of benefits and limitations that should be evaluated when making your decision. Careful consideration must also be given to factors like compressor efficiency, initial costs and maintenance needs in order to select an ideally suitable model that satisfies both your operational goals and budgetary constraints.
75 KW 100 HP Mobile Diesel Rotary Screw Truck Air Compressor 100 cfm 7/8/10/13 Bar Equipment Leasing
1. Compact and portable: The compact and portable design of the Jinjing brand diesel rotary screw air compressor for truck make
1. The original airend is sourced directly from Germany, ensuring top-notch engineering and quality.
2. The air produced is 100% oil-free and is certified by the renowned German organization TUV, ensuring the highest standards of purity.
3. Equipped with a centrifugal fan, this system offers a superior cooling effect, maintaining optimal performance and efficiency.
Jinjing brand reciprocating piston high pressure air compressors are widely used in precision machinery
11kw 0.7/0.8/1.0/1.3mpa Fix Speed screw air compressor For industrial workshops